
AlTiN: The Powerhouse for High-Heat and Tough Alloys
AlTiN (Aluminum Titanium Nitride) is a premium coating applied through a Physical Vapor Deposition (PVD) process. It is widely celebrated for its exceptional hardness, superior wear resistance, and remarkable thermal stability, particularly when confronting high-heat machining environments. The unique composition of AlTiN allows it to form a protective aluminum oxide layer at elevated temperatures, which acts as a formidable thermal barrier.
Key Benefits of AlTiN Coating:
-
Superior Hardness & Wear Resistance: AlTiN coatings are incredibly hard, providing robust protection against abrasive wear and leading to significantly extended tool life in challenging materials.
-
Outstanding Heat Resistance (Red Hardness): The formation of a stable aluminum oxide layer insulates the tool, effectively transferring heat into the chip rather than the end mill. This makes AlTiN an ideal choice for dry machining or applications where coolant use is limited.
-
Excellent for Ferrous Materials & High-Temp Alloys: AlTiN is a top performer for machining a wide range of ferrous materials, various stainless steel grades, and notoriously challenging high-temperature alloys (e.g., Inconel, Titanium alloys, other aerospace materials) due to its ability to withstand extreme temperatures and resist chemical reactions.
-
Improved Performance in Demanding Applications: It consistently maintains its hardness and cutting integrity even under high cutting speeds and heavy loads, facilitating higher material removal rates and boosting overall productivity.
Ideal Applications for AlTiN Coated End Mills:
-
Hardened Steels: Excellent for machining steels with high hardness, including tool steels and hardened alloy steels.
-
Stainless Steels: Highly recommended for various stainless steel grades where heat generation and wear resistance are critical concerns.
-
High-Temperature Alloys: Performs exceptionally well in superalloys and other difficult-to-machine aerospace materials.
-
Dry Machining: Its inherent high thermal stability positions it as a prime choice for operations where cutting fluids are not used or are intentionally minimized.

CVD Diamond: The Ultimate for Extreme Hardness and Abrasive Materials
CVD Diamond (Chemical Vapor Deposition Diamond) refers to a revolutionary coating that applies a layer of polycrystalline diamond directly onto a carbide end mill. Unlike other coatings, this is actual diamond, grown atom by atom, harnessing diamond's unparalleled hardness and wear resistance. The CVD process involves a high-temperature chemical reaction that ensures an exceptionally strong, integral bond between the pure diamond layer and the end mill's carbide substrate. This coating is specifically designed for the most demanding applications involving highly abrasive and difficult-to-machine non-ferrous materials.
Key Benefits of CVD Diamond Coating:
-
Unrivaled Hardness & Wear Resistance: CVD Diamond is the hardest and most wear-resistant coating available for end mills. It offers extreme protection against abrasion, even in the most aggressive and abrasive workpiece materials. This translates directly to significantly extended tool life and consistent performance where other tools would fail quickly.
-
Superior Abrasive Material Machining: Its diamond composition makes it the premier choice for cutting highly abrasive non-ferrous materials that rapidly wear down conventional or even other coated tools.
-
Exceptional Edge Retention: The inherent strength and stability of diamond ensure that the end mill's cutting edges remain incredibly sharp for much longer, providing consistent, precise cutting performance and superior surface finishes throughout the tool's life.
-
Reduced Friction & Heat Generation: Diamond naturally possesses a very low coefficient of friction. This property, when applied as a coating, helps to minimize heat buildup at the cutting zone, further prolonging tool life and improving chip evacuation, especially in materials prone to sticking.
Ideal Applications for CVD Diamond Coated End Mills:
-
Graphite Machining: The go-to choice for machining graphite electrodes for Electrical Discharge Machining (EDM) and other graphite components, offering vastly superior tool life and maintaining fine finishes.
-
Green Ceramics & Green Carbides: Perfectly suited for highly abrasive unsintered (green) ceramic and carbide materials, prior to their final sintering process.
-
Highly Abrasive Composites: Excels in machining advanced composite materials like Carbon Fiber Reinforced Polymers (CFRPs), Fiberglass, G10, and other fiber-reinforced plastics, where the abrasive fibers cause rapid wear on other tooling.
-
High Silicon Aluminum: While Amorphous coatings are excellent for many aluminum alloys, CVD Diamond is often the preferred choice for extremely high-silicon aluminum alloys that are particularly abrasive and challenging.
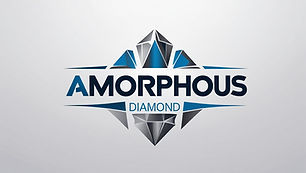
Amorphous: The Champion for Non-Ferrous and Abrasive Materials
Our Amorphous coating is a sophisticated solution that provides an exceptional combination of hardness and lubricity. Applied via Physical Vapor Deposition (PVD), this thin, smooth coating offers unique advantages, particularly when machining softer, gummy, or highly abrasive non-ferrous materials. This coating's amorphous (non-crystalline) structure is engineered to deliver properties akin to diamond-like hardness alongside low friction characteristics.
Key Benefits of Amorphous Coating:
-
Exceptional Lubricity & Low Friction: Amorphous coatings boast an incredibly low coefficient of friction, which dramatically minimizes heat generation at the cutting edge, effectively reduces built-up edge (BUE), and significantly promotes smooth, efficient chip evacuation. This results in cleaner cuts and superior surface finishes.
-
High Hardness (Diamond-Like Properties): This coating exhibits impressive hardness, providing outstanding wear resistance against abrasive workpiece materials.
-
Maintains Sharp Cutting Edges: The PVD application process allows for a very thin coating that precisely replicates the geometry of the end mill, crucially preserving the sharp cutting edges, which is vital for precision and achieving a high-quality finished surface.
-
Anti-Adhesion Properties: Its smooth, non-stick surface actively prevents workpiece material from adhering to the tool, a common and problematic issue when machining softer, gummy, or non-ferrous alloys.
Ideal Applications for Amorphous Coated End Mills:
-
Aluminum Alloys: The premier choice for machining all types of aluminum, including those with high silicon content, owing to its superior low friction and anti-adhesion properties that prevent gumming.
-
Other Non-Ferrous Metals: Excellent performance on materials such as copper, brass, bronze, magnesium, and zinc.
-
Abrasive Plastics & Composites: Provides outstanding wear resistance when machining highly abrasive materials like carbon fiber reinforced polymers (CFRP), fiberglass, and various engineering plastics.
-
Graphite & Green Ceramics/Carbides: Ideal for highly abrasive materials where diamond-like properties are essential for tool longevity.
-
Fine Finishes: The inherent lubricity and precise edge preservation significantly contribute to achieving exceptionally high-quality surface finishes.